MEMS automotive sensors drive the future of mobility
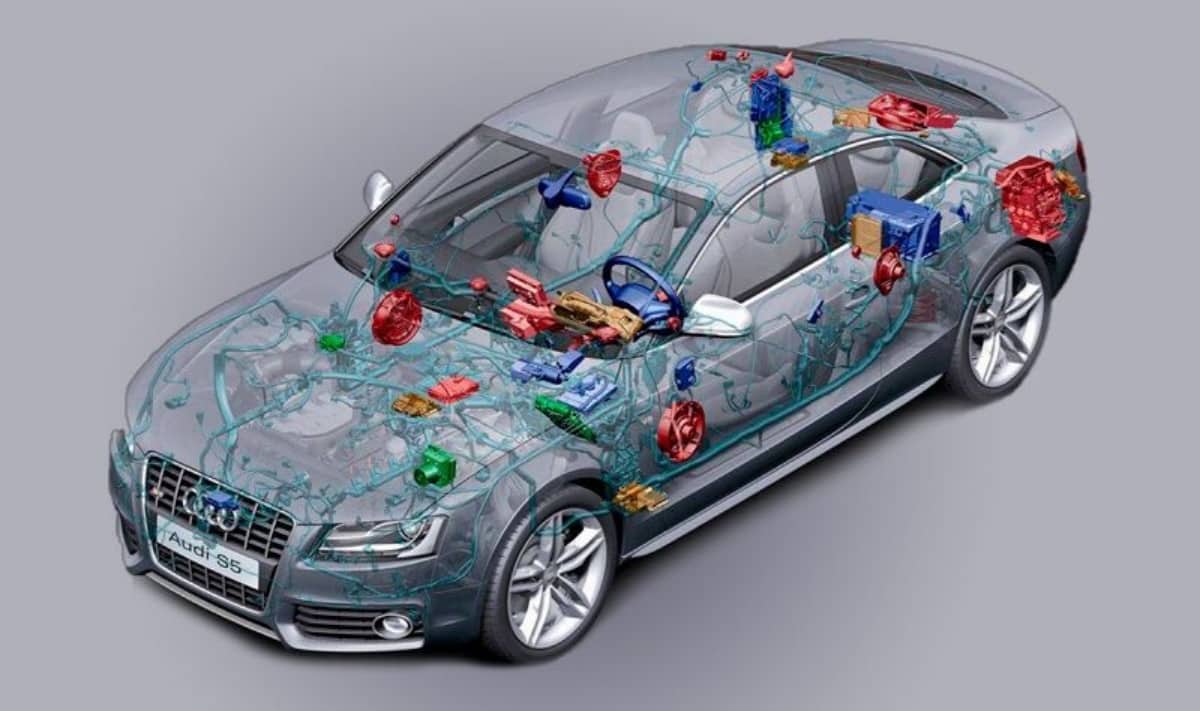
In this post, learn about
- The various kinds of MEMS sensors
- How MEMS sensors are deployed in automobiles
- MEMS sensors for auto safety
- MEMS sensors for engine and emission management
- MEMS sensors for driver comfort, convenience, and security
- The Future of automotive sensors
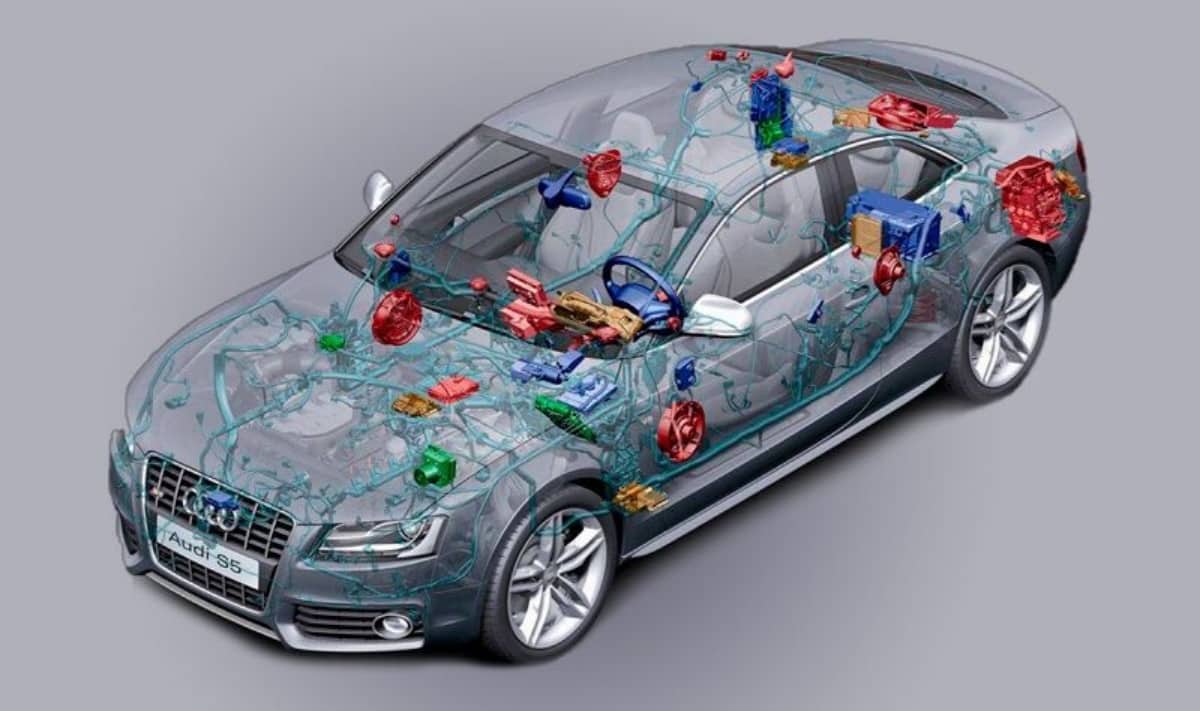
MEMS sensors have become essential in today’s automobiles by improving safety and stability, decreasing fuel use and emissions, and providing greater comfort and convenience for the vehicle’s occupants. MEMS sensors will be critical as the human driver increasingly relinquishes control to electronic systems, in tomorrow’s world of autonomous vehicles.
Microelectromechanical systems (MEMS) combine tiny mechanical parts, electrical devices, and electronic circuitry using integrated-circuit (IC) fabrication technologies. The structural features in these systems are quite small (ranging from 1 to 100 microns), with a typical MEMS chip varying from 1 to 5 millimeters. These devices vary from simple spring-and-weight mechanisms to complex systems with multiple moving components to devices with no moving parts at all.
Their small size provides great advantages over conventional sensor and actuator technologies, such as:
- Faster response times due to shorter electrical distances (within one chip, instead of across multiple discrete components)
- Lower power consumption
- Higher reliability, performance, and precision
- Significantly lower costs through mass manufacture using IC processes
Types of MEMS Sensors
Sensors detect and measure changes in environmental conditions such as pressure, acceleration, and electromagnetic energy and respond with electrical signals that can be used as input to controllers or actuators.
The MEMS sensors most prevalent in today’s vehicles are:
- Inertial sensors (accelerometers and gyroscopes)
- Magnetometers
- Pressure sensors
- Thermal sensors
- Gas sensors
- Optical MEMS
Inertial sensors include accelerometers and gyroscopes, whether individually or combined in packages. These sensors are the dominant type in the automotive industry and are used in many key applications.
Accelerometers measure static (gravity) and dynamic (motion or vibration) acceleration. MEMS accelerometers usually work on one of two principles: movement of a mass, or the piezoelectric effect. In the first principle, a weight is attached to a spring. Under acceleration, inertia tries to hold the mass in place, creating a force on the spring, which generates an electrical signal commensurate to the motion of the object. In the piezoelectric-based principle, the forces from acceleration act on a microscopic crystalline framework that generates a correlated voltage.
Gyroscopes (or gyros) identify angular change. MEMS gyros use paired vibrating objects like a tuning fork. Vibrating objects want to maintain their motion in the same plane. If the paired objects are accelerated linearly, then the two objects move in the same direction with no noticeable difference between the two in how they move. However, if the tuning fork is rotated, then a force acts on each object pointed in opposite directions. This is due to the Coriolis effect as the objects are forced to move out of plane. These forces can be converted into output voltages corresponding to the speed of the angular change.
A magnetometer measures the strength and direction of a magnetic field. A MEMS sensor typically relies on the Lorentz force, which is felt when a charged particle (as in an electrical current loop) passes through a magnetic field. The mechanical deflection of the electrical structure proportionate to the strength of the field can be discerned either electronically or optically.
MEMS pressure sensors assess the pressure difference across a silicon diaphragm. A fixed reference pressure is captured on one side of the diaphragm, while the other side is exposed to the environment to be measured. The effect on the diaphragm can be measured by the change in electrical resistance in the diaphragm materials due to mechanical strain (the piezoresistive effect mentioned above).
Thermal sensors measure temperatures. In MEMS, this sensing is typically accomplished using a resistance temperature detector. These detectors examine changes in the electrical resistance of a thin layer of test material (such as platinum, germanium, or polysilicon) in response to changes in temperature.
Gas sensors assess levels of gases such as carbon dioxide and other volatile compounds. There are a variety of detection technologies in use today, including electrochemical, pellistor, and photoionization methods.
Optical MEMS direct and detect light, from visible light to infrared wavelengths. Lens arrays and microscopic mirrors gather and direct light, while the detection of light intensity is handled with photodiodes (which generate an electrical current, when exposed to light) or photoresistors (which exhibit a change in electrical resistance under light).
Deployment of MEMS Sensors in Vehicles
MEMS sensors are widely used in vehicles today, and their array of applications is expanding. Although separate sensor, control, and actuator modules were common a few years ago, these functions are now being combined into micro integrated packages.
MEMS applications can be separated into three primary groups:
- Safety
- Engine/emissions management
- Security, comfort, and convenience
MEMS Type | Safety | Comfort | Engine Performance | Automotive Applications |
---|---|---|---|---|
Inertial sensors | • | • | Airbag, seat belt tensioner, rollover control, stability control, anti-lock braking, tire pressure monitoring, inertial navigation, emergency call system, electronic parking brake | |
Magnetometers | • | • | Anti-lock braking, stability control, tire pressure monitoring, camshaft/crankshaft speed and position | |
Pressure sensors | • | • | Tire pressure monitoring, fuel tank evaporation, exhaust gas recirculation, engine oil pressure, transmission oil pressure, brake booster, HVAC | |
Thermal sensors | • | • | • | Engine temperature, climate control, night vision display |
Gas sensors | • | • | Exhaust gas recirculation, HVAC | |
Optical MEMS | • | • | LiDAR, heads-up display, night vision display | |
Microphones | • | Voice-activated systems |
Safety
The increasing demand for robust and reliable vehicle safety systems has been and will continue to be a major factor in the growth of MEMS sensors in the automotive market.
The introduction and broad rollout of seat belts in the 1960s and 1970s and airbags in the 1980s and 1990s have resulted in significant reductions in injuries and fatalities from traffic accidents. The devices continue to evolve: cars now typically feature both front and side airbags, and many vehicles are fitted with seat belt pretensioners.
In an accident, the pretensioner spins the seat belt’s spool with an explosive charge to near-instantly draw up any slack in the belt. This action settles the car’s occupants solidly into their seats just before the full force of the impact hits, putting them into a position to gain maximum value from the ballooning airbag and to keep them from “submarining” under the bag and dashboard into the floor.
Accelerometers or inertial sensors and their associated electronics recognize any sudden deceleration from a frontal impact. In previous years, discrete accelerometers mounted at the front of the car communicated to electronics near the airbag. With MEMS technology, a tiny chip containing an accelerometer and microprocessor can be mounted near or within the airbag or seat belt pretensioner package. For side impacts, MEMS sensors evaluate a rapid increase in air pressure within the car door to decide whether the side airbags should be deployed. The fast response provided by MEMS is welcome considering that only milliseconds are available in which to trigger these safety devices and to protect the occupants.
Anti-lock braking systems keep the wheels rolling enough (even under heavy pressure from the driver on the brake pedal) to maintain control of steering while applying maximum stopping force without the tires slipping. Magnetic sensors determine which wheels are turning and at what speed, while gyros detect the rotation of the vehicle. The microprocessor then determines how much braking force each wheel should receive to help bring the vehicle under control.
Electronic stability control (ESC) combines input from gyros, accelerometers, and magnetic wheel speed sensors to recognize a skid or similar loss of control by comparing the car’s speed, motion (primarily the yaw, or spin around the car’s vertical axis), and steering angle. The ESC then adjusts the throttle and applies individual brakes as necessary to help the driver keep or regain control. With an effective ESC, the driver might not even be aware that the system was activated.
Sharp cornering and certain sudden steering actions can create the risk of rollover, especially in vehicles with a higher center of gravity such as SUVs, pickup trucks, and vans. Roll stability control combines the use of gyros and accelerometers to test whether the vehicle’s roll rate and angle have exceeded acceptable limits. If so, the controller may intercede to manage the brakes, throttle, engine torque, and/or active suspension systems (if available) to counteract the rollover forces. The system might also fire the side airbags if a rollover is imminent.
Tire pressure monitoring systems (TPMSs) help avoid unsafe driving conditions and poor fuel economy from tires that have lost significant pressure. Tire pressure can be monitored directly or indirectly. For direct measurement, a MEMS pressure sensor checks the inflation of each tire. In an indirect system, magnetic wheel speed sensors identify a wheel rotating faster than anticipated – an underinflated tire is a “smaller” tire and will have to rotate more often to keep pace with a properly inflated tire. In either case, the TPMS notifies the driver that there is a tire problem.
Adaptive cruise control and automatic emergency braking systems act on the driver’s behalf to adjust the vehicle’s throttle and/or apply the brakes, maintaining a safe distance from other vehicles and avoiding collisions. These systems rely on accurate distance measurements provided by technologies like LiDAR (light detection and ranging). LiDAR illuminates targets with pulsed laser light and determines the intervening distance based on the time required for the reflected laser light to return. By “painting” the environment in front of and around a vehicle in this manner, LiDAR can create a three-dimensional view of objects that the driver and automatic systems must be aware of. Optical MEMS, especially micromirrors, can play a necessary role in both the steering of the laser beam and the gathering of the reflected light.
Automatic emergency call systems combine input from inertial sensors and safety systems to determine whether an accident has occurred and, to some degree, the severity of the situation (e.g., have the airbags deployed?). The system can independently contact emergency services and, provide the accident’s location using navigational data. This can put first responders on the scene more quickly, especially when the vehicle’s occupants are unable to take action on their own.
Engine/emission management
Various sensors assist in maximizing engine performance and fuel efficiency while minimizing vehicle emissions.
Pressure and gas sensors monitor gases and fluids in and around the vehicle, including:
- Atmospheric pressure and air-fuel mixture, to ensure optimal fuel efficiency;
- Oil pressure, to maintain proper lubrication;
- Fuel tank pressure, to find potential vapor or fluid leaks; and
- Exhaust gas recirculation flow, to minimize NOx emissions.
Thermal sensors track engine temperature and prompt adjustments affecting performance (such as air-fuel mixture and ignition timing) and protection (cooling system).
Meanwhile, magnetometers gauge the speed and position of the camshaft and crankshaft to match the timing between valves and pistons and help manage effective fuel injection and consumption.
Comfort, convenience, and security
The driving public has an insatiable appetite for comfort, convenience, and security. MEMS sensors play a significant role in meeting the demand.
Drivers need not know how to reach their destination – they can hear step-by-step voiced instructions from the car’s GPS navigation system. However, GPS satellite signals are sometimes blocked by structures or dense foliage, causing a temporary disruption in data. Inertial navigation systems bridge that gap. MEMS inertial sensors track changes in speed and direction. This information is used by a processor to do “dead reckoning” calculations that predict the vehicle’s changing position until GPS is once again available.
Some automobiles now include the ability to hold a vehicle on a grade without the driver needing to hold the brake. This is a function of the electronic parking brake. This system senses an incline using data from MEMS accelerometers and holds the car temporarily from rolling. If the car is parked on a grade, the “hill hold” mechanism will keep the car from budging after the handbrake is released, freeing the driver from concern that the car will roll into any adjacent objects until the clutch is engaged and prepared to propel the vehicle forward.
The conditions within the vehicle can greatly affect occupant comfort. Climate control systems using MEMS thermal and gas sensors can monitor temperature, particulate matter, humidity, and carbon dioxide levels and adjust heating, cooling, and ventilation accordingly.
Anti-theft systems employ inertial sensors. These watch for a jostling of the car or for a new tilt that might come from an attempt to lift one end of the car. If such motion is found, the security system begins to wail and possibly transmits a radio signal calling for assistance.
What’s Next
The careful advancement toward self-driving cars will shape the future development of automotive MEMS. While some MEMS devices such as micromirrors provide support to autonomous vehicles (AVs), new ground must be broken.
AVs will rest heavily on optical and radio-frequency tools. Consider the snowballing of advanced driver-assistance systems like automatic emergency braking, adaptive cruise control, and lane departure warnings that will become steppingstones to fully functional AVs. Features such as these depend on fast, precise information generated by cameras, radar, and LiDAR, which are now finding their way into the microscopic scale of MEMS. In addition, MEMS are still at research stages for radio applications including dedicated short-range communications – wireless links to roadside or vehicle-to-vehicle infrastructures that will help manage AV traffic.
Conclusion
Currently, inertial applications implemented for safety are the largest role for MEMS sensors in the automotive field. However, their small size, reliability, low power demand, speed, and low cost make MEMS sensors attractive for broad use in vehicles for performance and convenience as well.
The evolution of autonomous vehicles will drive an even greater need for MEMS, especially those related to optics and radio frequencies. Companies breaking through these challenges will lead to a transformative period for MEMS.